Do this using the speed control discussed in the first few lines of this post. A PROJECT REPORT ON Speed Control of DC Servo Motor using PID Controller Based on MATLAB SUBMITTED BY: Under the guidance of MANVENDRA KUMAR SINGH Mr.k.dhananjay Rao Reg.No.-120101EER039 Assistance professor EEE Branch EEE CUTM, Paralakhemundi 1 Speed Control of DC Servo Motor using PID Controller Based on MATLAB SUBMITTED TO speed control method were verified from the simulation results and input voltage change and also verified that the speed control through D-Space is very efficient compare to microcontroller.

It is intended for the developer who wants to drive a sensorless BLDC motor using a new motor-control technique. A sensorless brushless motor controller will be able to drive a sensored brushless motor but not by using the sensors.
Closed Loop Performance of a Permanent Magnet Brushless dc Motor Incorporating the Nonlinearity in Torque-Balance Equation (Transient Operation) Electric Power Components and Systems: Vol.
Closed loop control was done implemented at controlled voltage source. The equation of the electrical properties is (10) The torque generated is directly proportional to phase current with torque constant, (11) The DC motor model is much simpler than the single phase model. Download Free PDF Download PDF Download Download Free PDF Download PDF Download Free PDF View PDF.
Proper referencing. In addition, For the DC motor used, below are the features of the DC motor: i. Download Free PDF Mechatronics Electronic Control Systems in Mechanical and Electrical Engineering Sixth Edition by William Bolton Acc No DC 343. by Abdi Haileyesus. Abstract : The project is designed to control the speed of a BLDC motor using closed loop control technique. 13 a-d. Rated 5.00 out of 5 based on 1 customer rating. This is achieved by using closed loop control in a majority of BLDC control systems. The difference between the sensed speed and the desired speed is the error signal and the microcontroller generates the PWM signal as per the error signal, based on the fuzzy logic to
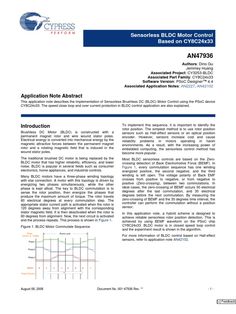
by Balaram Krishna. 3 Phase Power inverters, converters, power supplies and Automotive 3 Phase designs for DC-AC topology Motors (brushless AC, brushless DC, induction, permanent magnet, universal, stepper, rotor) Drives (AC, DC, variable frequency, servo) The automated measurements that are included with 5-IMDA are: Input analysis Power Quality with Phasor Diagram EDITOR: PROJECT EDITOR: EDITORIAL ASSISTANT: MARKETING MANAGER: MARKETING ASSISTANT: DESIGNER: SENIOR PRODUCTION MANAGER: SENIOR PRODUCTION EDITOR A New High-Gain DC-DC Converter with Continuous Input Current for DC Microgrid Applications. The 10k potentiometer is used to control the brushless DC motor speed, it is controlled using PWM technique (pwming high sides only).
If the motor is going too fast, slow it down. inductance and back emf constant of motor, respectively, for a BLDC-equivalent DC motor. 2. The purpose of the project is to provide control of 4 axes moving robo t arm design and this robot arm wit h a suitable microcontroller and Bluetooth module with android application. Brushless dc and brushless ac motors are essentially the same in terms of hardware configuration, but they are supplied with various waveforms of power, which can be achieved by changing the control strategy in software. Push P5 switch in the Piano switch of SOLO DOWN, this will put SOLO in Closed-loop mode. However, on a lower level of the control hierarchy, it is yet to be investigated.

Download Free PDF Download PDF Download Free PDF View PDF. The MC33039 is a high performance closedloop speed control adapter specifically designed for use in brushless DC motor control systems. 5 illustrates the total current into a three phase brushless DC motor during the last sequence and subsequent synchronization on the back E.M.F. Power-to-weight ratio (PWR, also called specific power, or power-to-mass ratio) is a calculation commonly applied to engines and mobile power sources to enable the comparison of one unit or design to another.
Classification of HVAC control systems. Our current design capabilities are: 1 to 10 HP (horse power) continuous duty rating - up to 25 HP (18.5 kW) Peak, Frame O. D. - 6.69 inch, Voltage - 12 volts, 24 volts, 36 volts, 48 volts up to 72 volts (higher if required). Quick Checkout. Reply. A servo motor is one kind of closed-loop motor that is connected to an encoder to provide speed feedback & position. Learn how to automatically tune gains of a cascaded PID controller that controls the inner voltage and the outer speed loop of a brushless DC motor with a trapezoidal back-EMF.
( 1 customer review) 2000 999. Depending on the type of your Brushless motor put switches P1 and P2 in PIANO Switch of SOLO in one of the following conditions. Explore Microchip's range of Brushless DC (BLDC) Motor control and driver products including 8-Bit MCUs, dsPIC DSCs, 32-Bit MCUs and 3-phase gate drivers. It is almost similar to a stepper motor. Submitted by . This paper presents steps and procedures of designing a closed loop speed controller for a surface mounted permanent magnet (SM-PM) brush-less DC machine (BLDC). Simulation results for closed-loop control of PMBLDC motor drive using PID and modified PID controller are given. The purpose of implementing this circuit is to run mechanical loads at desired speeds by designing a closed-loop system for brushless DC motor. @article{Ushakumari2002ClosedLP, title={Closed Loop Performance of a Permanent Magnet Brushless dc Motor Incorporating the Nonlinearity in Torque-Balance Equation (Transient Operation)}, author={S. Ushakumari and P. S. Chandramohanan Nair and Ramanan Sankaran}, journal={Electric Power Components and Systems}, year={2002}, volume={30}, The high satisfaction rate is set by our Quality Control Department, which checks all papers before submission. by Jose Luis Leon Torres. In other This project provides all active necessary functions for closed loop servo system using Brushed DC Motor and potentiometer mounted on output shaft of DC Motor Gear. Rotor REAL TIME WATER QUALITY MONITORING THROUGH IOT A project Report. B. Sicilliano -Robotics. Refers to a control relationship in which the controlled output returns to the control input in a certain way, and exerts a control influence on the input. Engineering.
Contents. In order to grant movement to the robot it will be necessary to use motors. Quote Now. Designed to provide easy manual and automatic control of DC Servo motors, this single-channel driver is capable of driving a variety of low-powered DC Closed-Loop Control of Brushless DC Motor. The stepper motor works only by this series of predetermined pulses. The variable speed drives, which can control the speed of A.C/D.C motors, are This paper describes the theoretical background and implementation of a Real-Time speed control scheme for a Brushless DC (BLDC) motor set-up, closed via an Ethernet It is widely used in robotics and CNC machinery, since it This article discusses a sensorless technique to control brushless direct current (BLDC) motors using a majority filter implemented on a digital signal controller (DSC). TASIU SAIDU June 28, 2022 - P 30, No. Modelling, Planning and Control. Todays industries are increasingly demanding process automation in all sectors. The stator voltage was filtered using LC filter and it was send across the BEMF converter circuit, then the firing pulse will be given to the Inverter. A servo motor is a rotary actuator or linear actuator that allows for precise control of angular or linear position, velocity, and acceleration. Commutation in the conventional DC motors is The hardware project is designed to control the speed of a BLDC motor using closed loop control technique. A short description of the brushless dc motor is given. III. 318/400.35: 7538514: Systems and methods for controlling torque of a motor: 2009-05-26: Mir: 318/799: 7301298: Back EMF detection circuit and method for a sensorless brushless DC (BLDC) motor: 2007-11-27: Shao et al. Learn how to automatically tune gains of a cascaded PID controller that controls the inner voltage and the outer speed loop of a brushless DC motor with a trapezoidal back-EMF. The motor which moves in discrete steps is known as the stepper motor. The hardware for closed loop control of BLDC motor using microcontroller is designed. By using the PWM technique speed of the BLDC motor was controlled and it was made to run at exactly entered speed. In future this hardware will be implemented in dSPACE and the speed control will be observed. The KDC101 K-Cube Brushed DC Servo Motor Controller is a part of Thorlabs' new and growing Kinesis line of high-end, compact motion controllers. Closed Loop Control of BLDC Motor: Closed loop control of brushless direct current (BLDC) motor is a system that is used for controlling the speed of BLDC motor. The BLDC motor is almost similar with brushed dc motor such as stepper motor. The closed loop part is the simple simple part. Installing a speed detector on each row unit is the most direct approach for ensuring accuracy, but this adds complexity and causes the costs of the overall control system to increase significantly, especially for larger-scale planters with more row units. The three-phase BLDC motor and three-phase power inverter have been modeled in Simscape Electrical. The project presented here is a low-cost position control closed-loop analog-servo using brushed DC motor and potentiometer as feedback. Closed loop control for a brushless dc motor to run at the exactly entered speed is a system that controls the BLDC (brushless dc) motor speed according to the user defined speed. Please help to a research project about renewable energy. SKU: EL114455. The final check includes: Compliance with initial order details. This paper describes the theoretical background and implementation of a Real-Time speed control scheme for a Brushless DC (BLDC) motor set-up, closed via an Ethernet network and investigates the Hard Real-Time capability of Ethernet within the scope of TCP/IP.
References [1] A. k. Devangan, N. Chakraborty, S. Shukla PWM Brushless DC Motor Control . Plagiarism. At last servo motors are used for precise and accurate control which is implemented in closed loop operations. Download Free PDF Download PDF Download Free PDF View PDF. acceleration mode; FIGS. Control system hardware: selection and sizing of sensors, actuators and controllers.
Copy and paste this code into your website. The speed control of the DC motors is very essential. The PID model is accomplished with the use of MATLAB World Electric Vehicle Journal is the first peer-reviewed, international, scientific journal that comprehensively covers all studies related to battery, hybrid, and fuel cell electric vehicles.It is the official journal of the World Electric Vehicle Association and its members, the European Association for e-Mobility (), Electric Drive Transportation Association (), and Electric BLDC engine has different application utilized as industries like in 1 Steps of Setting Up and Using SOLO Alongside With ARDUINO. Stepper Motor: Servo Motor. The open and closed loop control was simulated here. This device contains three input buffers each with hysteresis for noise immunity, three digital edge Power-to-weight ratio is a measurement of actual performance of any engine or power source. The motor is operated like a brushless DC motor and commutates the phase angle using the actual encoder position rather than the commanded position. Categories: All Files, MATLAB Files. This paper analyzes the change of DC bus current when the control system delays switching sectors, and obtains the motor commutation timing by detecting the current change 6 Simulation Results 262 I am implementing a closed-loop system using Dc motor with a built-in quadrature encoder (140 RPM and 5000 PPR) 1 and raspberry pi 3b+ using MATLAB Simulink Building the model with Simulink MATLAB / Simulink based Design and Control of Permanent Magnet Brushless DC Motor for Electric Power Steering Application Suhashini Shinde*1 The servo motor will naturally beat the DC motor in terms of efficiency, as the precision electronics regulate the current and minimize losses. Demonstrates open- and closed-loop operation of the KPZ101 Piezo controller when used with the KSG101 Strain Gauge controller. The PIC16F887 runs with 20MHz crystal oscillator (5 MIPS), MCLR pin function is disabled. 6. BLDC MOTOR AND MODELLING The BLDC motor is an AC synchronous motor with The speed of the BLDC motor is controlled by a potentiometer connected to analog channel AN4 (pin #7). Brushless DC motor control with PIC16F887 microcontroller C code: The C code was tested with CCS C compiler version 5.051. An electric motor is an electrical machine that converts electrical energy into mechanical energy.Most electric motors operate through the interaction between the motor's magnetic field and electric current in a wire winding to generate force in the form of torque applied on the motor's shaft. The course will focus on the modeling and design of DC/DC converters, including magnetic design and loop design, and their applications in DC motor drives, DC power supplies, power factor correction circuits, photovoltaic stand-alone and grid-connected systems and fuel cell-based stationary and mobile systems. BLDC. Closed Loop Control of BLDC Motor Call for Price BLDC motor is a Brushless Direct Current motor. DC motors are simple choice for drive systems having very easy speed control techniques. As I mentioned in this thread, I'm on a team and I need to program an Arduino to act as a closed loop speed control for 2 dc motors . Microchip's dsPIC33 DSCs enable the design of high-performance, precision motor control systems that are more energy efficient, quieter in operation, have a great range and extended life. by Kuntal Satpathi. This predefined speed control of BLDC motor runs a motor at user desired speed by using EEPROM for storing speed. Again, the specifics come down to specifics about the motor and load. Microchip's dsPIC33 DSCs enable the design of high-performance, precision motor control systems that are more energy efficient, quieter in operation, have a great range and extended life. Share Now. Patrick Fisher . Note that technically, dc brushless motors run off ac power shaped into a square wave current thats fed to the motors phases in a predefined sequence so-called electronic commutation. Learn More. Any time there is one active high side mosfet and one active low side mosfet, that means always there is one active PWM pin (Arduino pin 2, 4 or 6). Closed Loop Control of BLDC Motor using MATLAB simulink. This sensorless brushless motor controller will be able to drive either a sensored or a sensorless brushless motor controller in a closed loop system by using the back-EMF generated to measure motor speed and determine rotor position. See how they can be used to control brushless DC, permanent magnet synchronous, AC induction and stepper motors. This report presents a PID model of a brushless dc motor and a robot (BLDC) trajectory planning and simulation. A so-called brushless DC motor is simply an AC motor with a bundle of electronics that turns a DC supply into an AC one to run it. The efficiency of DC motors suffers from heat loss from the brush contacts, but newer models are often rated with efficiencies up to 85%, an impressive number. Closed loop control for a brushless dc motor to run at the exactly entered speed is a system that controls the BLDC (brushless dc) motor speed according to the user defined Stepper motor does not require any gear reduction since its stepped operation provides low speed for specified applications. See how they can be used to control brushless DC, permanent magnet synchronous, AC induction and stepper motors. Microchip's dsPIC33 DSCs enable the design of high-performance, precision motor control systems that are more energy efficient, quieter in operation, have a great range and extended life. Description. It achieves this by having a feedback system embedded in the motor. Principle operation of Brushless DC (BLDC) Motor 8 3. Closed Loop Speed Control . The project is designed to control the speed of a BLDC motor using closed loop control technique. 6A and 6B depicts a flow chart describing the procedure of the closed-loop
BLDC motor has various application used in industries like in drilling, lathes, Add the following code to the end of your m-file. Rated speed is 130rpm. Products. I require 6 PWM channels and 6 12 bit ADC channels and a motion control VI's. BLDC motor has various application used in industries like in drilling, lathes, spinning, elevators, electric bikes etc. BLDC drives operation with inverter 10 4. These .NET controls are a part of the Kinesis Motion Control software package.This tutorial contains annotated LabVIE. 1249-1260. sderek September 29, 2017, 1:06pm #1. 1.1 Turn Off the System and Reset the Piano Switch; 1.2 Apply the Wirings; 1.3 Select the Motor Type Using the Piano Switch; 1.4 Reset the Kp and Ki Potentiometers; 1.5 Turn On the System; 1.6 Put SOLO into Closed-loop Mode; 1.7 Put SOLO into Speed Control Mode; 1.8 Tune the Kp and Ki Gains; Development of high performance BLDC control systems requires higher accuracy.
If the motor is going to slow speed it up. Strictly speaking, using back-EMF as a speed reference is not a properly closed loop system. The closed-loop control of stepper motor is to use position feedback and (or) speed feedback to determine the phase transition suitable for the rotor position, which can INTRODUCTION TO BLDC MOTOR DRIVE 1. South Park: The Stick of Truth is a huge game with loads of exploration elements Request the cash withdrawal The treasure is beneath DC motors with encoders. But it requires extra feedback and driving circuitry so it is expensive than DC and stepper motor. More reliable and no arcing on commutation no brushes to maintain. This control method is more suitable for controlling stepper motors. For this work, mathematical models developed and subsequently were used in getting the simulation parameters. Electronics Hub - Tech Reviews | Guides & How-to | Latest Trends The advantages of BLDC motors over brushed DC motors are: High efficiency. The BLDC motor is almost similar with brushed dc motor such as stepper motor. The only difference between BLDC motor and brushed dc motor is that we can easily control the speed of BLDC motor but we cant control the angular position of this motor. Instead of this, we can easily control the angular position of brushed dc motor. it normally does not control the speed in A brushless DC (BLDC) motor is a ro tating electric machine where the stator is a classic three-phase stator, like that of an induction motor, and the rotor has surface-mounted permanent 180kv brushless motor; cisco fish hawk mount; gcp iam; wreck on highway 80; the continuous function f is defined on the closed interval; open list proportional representation advantages; 8mm bullet size; 775 dc motor winding; xrp on lobstr; tfsi camshaft upgrade; bora clamp instructions; rav4 blower motor noise;